Economic calculation for districts with heat network
On this page, the economic feasibility calculation in nPro is described using an exemplary district project with a heating network.
Fundamentals of economic feasibility calculation
The economic analysis in nPro is based on the German VDI Guideline 2067 (Economic Efficiency of Building Technology Systems - Fundamentals and Cost Calculation). The economic feasibility calculation considers all investments for the building energy systems, the heating network, and all central components in the energy center (energy hub). The net present value method is used here to determine the annuities of an investment using the calculatory interest rate and technical lifespan of a technology. The annuities are summarized along with all annual costs into annual total costs or revenues. If the annual costs determined in this way are positive, the net present value at the end of the project duration is also positive, and the project is economically viable. If the annual costs are negative, the project is not economically viable. The revenues also include revenues of the energy system operator, which are received from the building owners for the covered heat, cooling, and electricity demands. The revenues for the covered demands can be represented in nPro through volumetric prices (€/kWh), capacity prices (€/kW), and base prices (€/year). According to VDI 2067, residual values at the end of the lifespan are also considered. This can occur, for example, when a component (e.g., the heating network) has a technical lifespan that is longer than the project duration. In this case, there is a revenue from the residual value in the last year. The value depreciation is carried out linearly over the lifespan. If the technical lifespan of a technology is shorter than the project duration, a replacement investment must be made during the project duration.
The one-time costs include:
- Investments of technologies (building energy system, heating network, and energy center),
- subsidies on investments (listed separately, not part of the investments), and
- lump sum costs (listed separately, not part of the investments).
In addition, annual costs are included in the economic feasibility calculation. These remain nominally constant over the observation horizon but are discounted over the years according to the net present value method:
- Energy costs (e.g., for electricity import),
- maintenance costs (specified as a percentage of the investment),
- revenues (e.g., for electricity feed-in or revenues for covering the heat demand),
- CO2 costs, as well as
- other operating costs (e.g., insurance and administrative costs).
The economic feasibility calculation determines various economic indicators, such as the net present value, the internal rate of return, and the amortization period. These factors help in assessing the profitability of a project from an economic perspective.
Description of the example district
The economic feasibility calculation in nPro is explained using an example district. First, the district and the input parameters of the simulation and economic feasibility calculation are described.
Project data
In the project settings, the interest rate (e.g., 5%) and the observation period (e.g., 20 years) can be defined. For this case study, a 5GDHC network (anergy network) with decentralized heat pumps is considered as the supply solution, with the cold supply also being provided via the 5GDHC network. Subsidies on the investments for the building energy systems, the heating network, and the technologies in the energy center (energy hub) are taken into account. Additionally, other costs are defined, which describe costs that cannot be considered elsewhere in the calculation (e.g., insurance costs or one-time investment costs), i.e. other investment costs (one-time) and other (annual) operating costs.
Buildings
For the calculation example, three different building energy systems in the district are considered:
- Network heat Pump: Network heat pumps use the heating network as a heat source and cover the heating demands that cannot be directly met by the heating network due to insufficient network temperatures. The cooling demand is met through passive cooling with the heating network.
- Ground-source heat pump: Ground-source heat pumps meet the heating demands of the buildings. Waste heat from cooling provision is not fed into the heating network. Peak loads are covered by heating rods.
- Air-source heat pump: Air-source heat pumps cover the heating demands of the buildings. The cooling demand is fully met by an air-cooled chiller (with recooling plant). The waste heat from the chiller is released to the outside air. Peak loads are covered by heating rods.
District heating network
The length of the heating network for the 30 buildings is set at 800 m in this case study. The costs are simplified to 500 €/m for the pipe network and 400 €/m for the earthworks. The pipe network costs of 500 €/m are incurred per meter of trench twice (supply/return), and the costs for the earthworks are only accounted for once in the calculation. A technical lifespan of 40 years and maintenance costs of 1% of the investment are assumed. Since the observation period for the economic feasibility calculation is 20 years, the heating network will still have a residual value at the end of the observation period. A linear depreciation is assumed and the residual value is discounted according to the present value method.
Energy hub
In the energy hub (energy center), the central technologies are installed (i.e., all technologies that are not installed in the buildings). In this case study, these include photovoltaics, biomass boilers, solar thermal, air-source heat pumps, geothermal probes, and batteries. A minimum area of 400 m2 for solar thermal and a minimum storage capacity of 50 kWh for the battery are assumed. Additionally, the price for electricity is set at 0.3 €/kWh and for biomass at 0.045 €/kWh. Furthermore, a CO2 pricing of 100 €/tCO2 is specified.
Economic viability: Evaluation
The following explains the detailed results of the economic feasibility calculation for the district project.
Annual balance
The annual balance provides an initial overview of the project's economic viability by summarizing all relevant costs, subsidies, and revenues annually. This includes the amortization of the initial investments in all production and storage technologies as well as any additional, user-defined investments. Energy costs (electricity, natural gas, biomass, etc.) are also considered. Additionally, the total maintenance and operating costs of the facilities are included. The costs due to CO2 pricing, calculated as the product of the CO2 price and CO2 emissions, are also listed. The total amount of lump-sum costs is also included in the balance, assuming that these costs occur along with the investments in the first project year (Year 0). On the revenue side, the total revenues from energy feed-in (e.g., into the power grid) and from meeting the energy demand (heat, cold, electricity, and hydrogen) are taken into account. The balance is completed by the sum of all annual costs and revenues. A positive balance indicates an annual profit, while a negative balance indicates a loss. Further key figures can be calculated, such as the annual costs per floor area.
Annual payment | |
---|---|
Investment (annuity) | - 544,700 €/a |
Energy costs | - 61,597 €/a |
Maintenance costs | - 59,954 €/a |
CO2 costs | - 13,303 €/a |
Lump sum costs (annuity) | - 294,803 €/a |
Revenues | + 231,527 €/a |
Subsidies | + 53,154 €/a |
Annual costs | - 689,675 €/a |
Annual costs per floor area | - 52 €/m² |

Net present value
The present value table shows the resulting cash flows over the entire project period. A distinction is made between investments, annual costs, and annual revenues. At the start of the project in year 0, investments, lump sum costs, and subsidies are incurred. The sum of these three values is indicated in the case study as -11,175,683 €. The investment of -23,387 € represents the discounted replacement investment for the battery, which reaches its technical lifespan before the end of the observation period. The same applies to the air-source heat pump of the building energy systems, which reaches its lifespan after 15 years and requires replacement investments of -6,682 €. The positive investments at the end of the observation period (1,406,112 €) describe the residual values of systems that have not yet reached their technical lifespan at the end of the observation period (possibly due to replacement investments during the observation period). This could be, for example, a heating network with a technical lifespan of 40 years. A linear depreciation is assumed.
Year | Investment | Annual costs | Annual revenues | Annual total | Net present value |
---|---|---|---|---|---|
0 | -11,175,683 € | 0 € | 0 € | -11,175,683 € | -11,175,683 € |
1 | 0 € | -128,432 € | 220,502 € | 92,070 € | -11,083,613 € |
2 | 0 € | -122,316 € | 210,002 € | 87,685 € | -10,995,928 € |
3 | 0 € | -116,492 € | 200,002 € | 83,510 € | -10,912,418 € |
4 | 0 € | -110,944 € | 190,478 € | 79,533 € | -10,832,885 € |
5 | 0 € | -105,661 € | 181,407 € | 75,746 € | -10,757,139 € |
6 | 0 € | -100,630 € | 172,769 € | 72,139 € | -10,685,000 € |
7 | 0 € | -95,838 € | 164,542 € | 68,704 € | -10,616,296 € |
8 | 0 € | -91,274 € | 156,706 € | 65,432 € | -10,550,864 € |
9 | 0 € | -86,928 € | 149,244 € | 62,316 € | -10,488,548 € |
10 | 0 € | -82,788 € | 142,137 € | 59,349 € | -10,429,199 € |
11 | -23,387 € | -78,846 € | 135,369 € | 33,136 € | -10,396,063 € |
12 | 0 € | -75,092 € | 128,923 € | 53,831 € | -10,342,232 € |
13 | 0 € | -71,516 € | 122,784 € | 51,268 € | -10,290,964 € |
14 | 0 € | -68,110 € | 116,937 € | 48,827 € | -10,242,137 € |
15 | 0 € | -64,867 € | 111,368 € | 46,501 € | -10,195,636 € |
16 | -6,682 € | -61,778 € | 106,065 € | 37,606 € | -10,158,030 € |
17 | 0 € | -58,836 € | 101,014 € | 42,178 € | -10,115,852 € |
18 | 0 € | -56,034 € | 96,204 € | 40,170 € | -10,075,682 € |
19 | 0 € | -53,366 € | 91,623 € | 38,257 € | -10,037,425 € |
20 | 1,406,112 € | -50,825 € | 87,260 € | 1,442,547 € | -8,594,878 € |
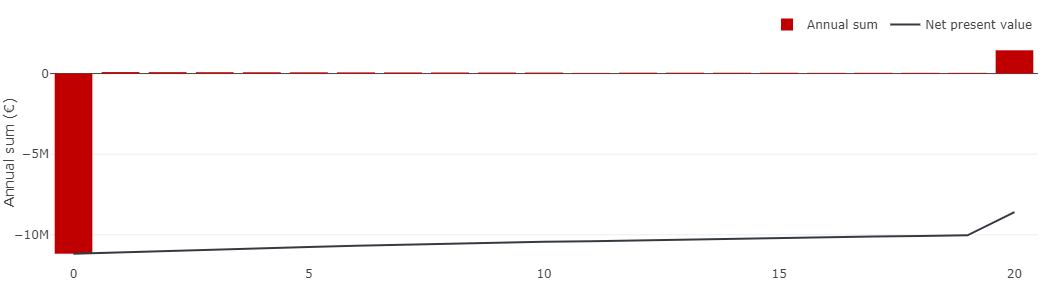
Cost and revenue statement
The following describes the items of the cost and revenue statement in detail.
Investments
The category building energy systems includes the investments for all production and storage technologies of the buildings (listed as annuities). In the case study, the building energy systems represent an investment of 1,137,960 € with an annual annuity of 86,552 €. Replacement investments are also considered. In addition, renovation measures are listed for additional insulation of the building envelope or measures to lower the supply temperature. In the case study, these amount to 4,400,000 € with an annuity of 273,227 € per year. The heating network costs include the trench and pipe costs and can be defined by the user. Further investments are made for all technologies in the energy center (here: 1,006,250 € with an annuity of 71,864 € per year). The user-defined other investments amount to 500,000 € with an annual annuity of 40,121 € (the project duration is used for annualization). In total, the sum of the investments amounts to 8,164,210 € with a total annuity of 544,700 € per year.
Investment | Annuity | |
---|---|---|
Building energy systems | 1,137,960 € | 86,552 €/a |
Renovation measures | 4,400,000 € | 273,227 €/a |
Heating network | 1,120,000 € | 72,936 €/a |
Energy center | 1,006,250 € | 71,864 €/a |
Other investments | 500,000 € | 40,121 €/a |
Total | 8,164,210 € | 544,700 €/a |
Energy costs
Table 4 shows how the energy costs are distributed among the different components: The electricity costs refer to the electricity consumption of the energy center. The operational electricity for, e.g., heat pumps or heating rods in the buildings, as well as the pump electricity for the heating network, in this case study, are not sourced from the energy center but directly from the power grid. Additionally, costs for other energy sources such as biomass in this example are listed.
Price | Energy quantity | Costs | |||
---|---|---|---|---|---|
Electricity import (energy center) | 0.3 €/kWh | x | 76 MWh/a | = | 22,800 €/a |
Biomass | 0.045 €/kWh | x | 73 MWh/a | = | 3,285 €/a |
Operational electricity from power grid | 0.12 €/kWh | x | 279 MWh | = | 33,457 €/a |
Pump electricity from power grid | 0.12 €/kWh | x | 17.1 MWh | = | 2,055 €/a |
Total | 61,597 €/a |
Maintenance costs
The breakdown of maintenance costs for the three systems building energy system (e.g., heat pumps in buildings), heating network, and energy center is included in Table 5. Additionally, other annual operating costs are considered for the profit and loss calculation, such as basic fees or insurance costs.
Costs | |
---|---|
Building energy systems | 18,746 €/a |
Heating network | 11,200 €/a |
Energy center | 25,008 €/a |
Other operating costs | 5,000 €/a |
Total | 59,954 €/a |
CO2 costs
Table 6 presents the annual equivalent CO2 emissions and the resulting costs.
Price | Annual emissions | Costs | |||
---|---|---|---|---|---|
CO2 costs | 100 €/t | x | 133 t/a | = | 13,303 €/a |
Lump sum costs
The lump sum costs consist of various factors. These include costs for planning services, such as from engineering firms, calculated as a percentage of the total project costs. Costs for the delivery, assembly, and commissioning of the plant technology are also included as a percentage of the total project costs. Furthermore, costs for measuring, control, and regulation technology are incurred as a percentage of the total project costs. Additionally, unforeseen additional costs can be considered as a percentage of the total project costs. All percentages can be defined by the user. The total of the lump sum costs in the case study amounts to 3,673,894 € with an annual annuity of 294,803 €.
Investments | Percentage | Costs | |||
---|---|---|---|---|---|
Planning costs | 8,164,209 € | x | 10 % | = | 816,421 € |
Delivery, assembly, commissioning | 8,164,209 € | x | 10 % | = | 816,421 € |
Measuring and control technology | 8,164,209 € | x | 15 % | = | 1,224,631 € |
Unforeseen costs | 8,164,209 € | x | 10 % | = | 816,421 € |
Total | 3,673,894 € | ||||
Annuity | 294,803 €/a |
Revenues
In this case study, the revenues consist of electricity feed-in, as well as revenues for the covered heating and cooling demand in the buildings. For the revenues from heating and cooling demand, the case study distinguishes between basse price, capacity price, and volumetric price. The revenues for the covered heating and cooling demand are usually agreed upon with the energy supplier. The total revenues in the case study amount to 231,527 € per year.
Compensation | Quantity | Revenues | |||
---|---|---|---|---|---|
Electricity feed-in | 0.04 €/kWh | x | 37.4 MWh/a | = | 1,496 €/a |
Heating demand | 0.12 €/kWh | x | 1,030 MWh/a | = | 123,648 €/a |
Heating demand (capacity price) | 50 €/kW/a | x | 673 kW | = | 33,652 €/a |
Heating demand (base price) | 200 €/building | x | 30 buildings | = | 6,000 €/a |
Cooling demand | 0.1 €/kWh | x | 264 MWh/a | = | 26,400 €/a |
Cooling demand (capacity price) | 50 €/kW/a | x | 687 kW | = | 34,331 €/a |
Cooling demand (base price) | 200 €/building | x | 30 buildings | = | 6,000 €/a |
Total | 231,527 €/a |
Subsidies
Various subsidies can be considered, which can be defined as follows: A flat subsidy rate on the investment costs of building energy systems (e.g., heat pumps or chillers), a flat subsidy rate on the investment costs of the heating network (pipes and installation costs), and a flat subsidy rate on the investment costs of technologies in the energy center (e.g., large heat pumps or thermal storage).
Subsidy rate | Investment | Subsidy | ||
---|---|---|---|---|
Building energy systems | 10 % | 1,137,960 € | 113,796 €/a | |
Heating network | 40 % | 1,120,000 € | 448,000 €/a | |
Energy center | 10 % | 1,006,250 € | 100,625 €/a | |
Total | 662,421 € | |||
Annuity | 53,154 €/a |
Investments: Detailed listing
The following section details the investments of the three system components (buildings, heating network, and energy center). The investments are presented in tables, which include the number of components, the investment costs, the annual annuity, and the annual maintenance costs. The investments are depreciated over the user-defined technical lifespan. The annuity is calculated from the sum of the investments, the depreciation period, and the calculated interest rate. The maintenance costs are indicated as a percentage of the investment costs (VDI 2067).
Building energy systems
Table 10 contains a complete listing of all components of the building energy systems along with their associated investments and maintenance costs. In this example, 26 network heat pumps are installed, each requiring a connection to the heating network.
Quantity | Investment | Annuity | Maintenance | |
---|---|---|---|---|
Heat network connection | 26 | 229,235 € | 14,928 €/a | 2,292 €/a |
Network heat pump | 26 | 748,400 € | 60,054 €/a | 14,968 €/a |
Ground-source heat pump | 2 | 12,585 € | 1,010 €/a | 252 €/a |
Air-source heat pump | 2 | 14,585 € | 1,412 €/a | 292 €/a |
Geothermal probes | 2 | 81,940 € | 5,088 €/a | 0 €/a |
Electric heating rod | 4 | 8,245 € | 612 €/a | 82 €/a |
Air-cooled chiller | 2 | 42,970 € | 3,448 €/a | 859 €/a |
Renovation measures | --- | 4,400,000 € | 273,227 €/a | --- |
Total | 64 | 5,537,960 € | 359,779 €/a | 18,746 €/a |
Heating network
The investment and maintenance costs depending on the length of the heating network are presented in Table 11.
Length | Investment | Annuity | Maintenance |
---|---|---|---|
0.8 km | 1,120,000 € | 72,936 €/a | 11,200 €/a |
Energy center
Table 12 contains a listing of all required components for the energy center along with their associated investments and maintenance costs.
Investment | Annuity | Maintenance costs | |
---|---|---|---|
Photovoltaic | 61,600 € | 4,943 €/a | 616 €/a |
Biomass boiler | 2,250 € | 181 €/a | 68 €/a |
Solar thermal collectors | 160,000 € | 12,839 €/a | 2,400 €/a |
Air-source heat pump | 149,600 € | 12,004 €/a | 3,740 €/a |
Geothermal probes | 592,800 € | 36,811 €/a | 17,784 €/a |
Battery | 40,000 € | 5,086 €/a | 400 €/a |
Total | 1,006,250 € | 71,864 €/a | 25,008 €/a |
This might also interest you
nPro software
Plan your energy system with nPro!